As hardware startups navigate the stages of development to decline, the importance of quality undergoes a dynamic transformation. During this process, quality control (QC), quality assurance (QA), and quality management (QM) each play a distinct role at each stage.
By understanding the evolving nature of quality throughout the product development lifecycle, hardware startups can effectively navigate the challenges and deliver products that meet customer expectations and drive business success.
Quality throughout the stages:
- Early Development Stage
- Late Development Stage or Pre-production
- Production and Manufacturing Stage
- Post-production and Customer Support
- Product Maintenance and End-of-Life
1. Early Development Stage:
During the early development stage, a hardware startup's focus should be on developing a proof of concept or prototype.
Even from this early stage, product quality remains crucial. A significant amount of time and resources can be saved later in the development process by finding and fixing design faults or functionality problems early on.
- Quality Control (QC):
QC at this stage entails running preliminary tests and inspections to spot any significant design faults or problems that might affect how the product develops. This reduces the possibility of creating a defective product from the beginning by identifying serious quality issues early.
- Quality Assurance (QA):
QA activities focus on setting quality goals, defining quality standards, and establishing quality processes and metrics. It ensures that the development efforts align with the desired quality goals and helps in building a solid foundation for future stages.
2. Late Development Stage/Pre-Production:
Ensuring the product meets the requirements and quality standards becomes more crucial as the product design completes. Before going into production, it is important to address any remaining manufacturing or design defects.
- Quality Control (QC):
This stage of quality control involves more thorough testing, inspections, and quality checks. It aims to identify and solve any unresolved design or production problems so that the product meets the quality requirements prior to production.
- Quality Assurance (QA):
At this stage, QA focuses on doing audits, reviewing documentation, and verifying that all quality processes and standards are being followed. It ensures that the product is ready for production by assessing its compliance with the defined quality objectives.
3. Production and Manufacturing Stage:
This stage is critical for maintaining consistent quality and ensuring that each manufactured unit meets the desired quality standards. Delivering a high-quality product to customers is essential for building a strong reputation and ensuring customer satisfaction.
- Quality Control (QC):
The focus of quality control (QC) activities now shifts to testing and inspecting the manufactured products to find any flaws or deviations from specifications. Prior to the product reaching the clients, it must undergo stringent quality inspections to identify and correct any problems.
- Quality Assurance (QA):
To ensure the appropriate level of quality, QA operations concentrate on monitoring and supervising the production processes. It involves implementing quality control procedures, monitoring quality metrics, and conducting frequent audits to ensure that the product consistently meets the defined quality standards.
4. Post-Production and Customer Support:
Maintaining high standards is essential, even after the product has been put on the market. For long-term profitability and client loyalty, it's crucial to focus on any post-production quality issues and customer satisfaction.
- Quality Control (QC):
QC activities in this stage involve analyzing customer feedback and addressing any reported quality issues promptly. This may include product returns, repairs, or replacements to maintain customer satisfaction and trust.
- Quality Assurance (QA):
QA activities focus on continuous improvement by analyzing customer feedback, identifying areas for enhancement, and implementing corrective actions. It aims to prevent future quality issues and enhance the overall customer experience.
5. Product Maintenance and End-of-Life:
Even as the product reaches the end of its lifecycle, maintaining quality remains important. Managing any remaining inventory and providing support for existing customers is crucial to uphold the brand's reputation and ensuring customer loyalty.
- Quality Control (QC):
QC activities during this stage involve ensuring the quality of the remaining products, mainly if they are being sold at a discounted price or through clearance sales. It aims to minimize any quality issues that may arise due to aging or obsolescence.
- Quality Assurance (QA):
The main goal of quality assurance operations is to control the product's end-of-life procedures, such as handling product recalls, discontinuation, or upgrading to newer versions. Customers should have a seamless transition, and any potential quality concerns should be minimized.
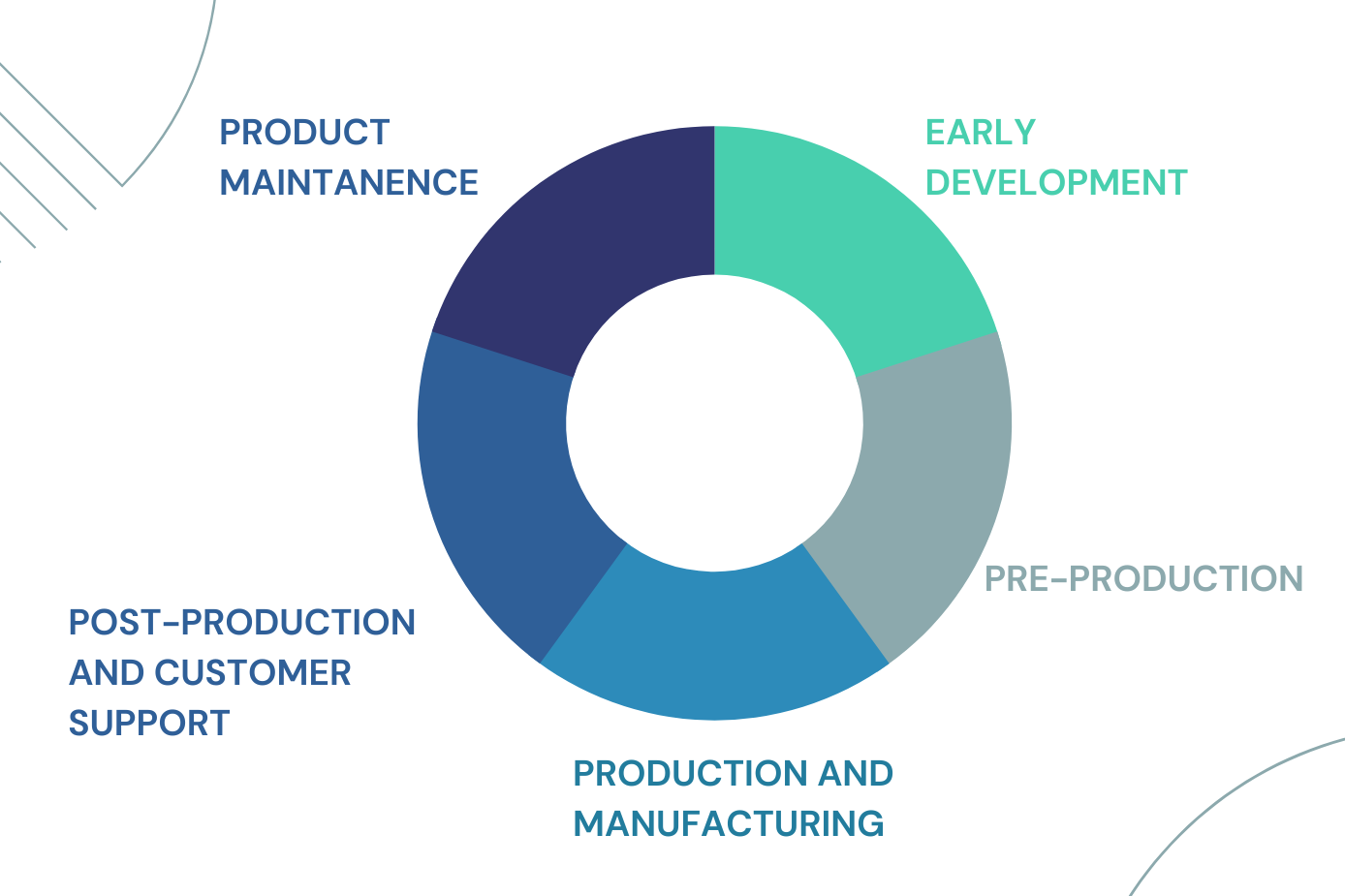
In conclusion, quality becomes more significant as a hardware company moves through the stages of product development. While QA defines quality standards and monitors process compliance, QC focuses on locating and resolving quality concerns. Planning, control, assurance, and improvement are all included in the larger approach to managing quality throughout the product's lifecycle known as QM.
At each stage, the exact tasks and priorities of QC, QA, and QM vary, but their ultimate goal is to provide a high-quality product that lives up to customer expectations.