
Image source
-
Natural Rubber (NR), also known as Isoprene or latex (working temperature: 0 ~ 80℃) is applicable to water and oil-free air, but not to petroleum products.
-
Silicone Rubber (working temperature: 7 ~ 260℃) is applicable to water, oil-free air, and high-temperature steam, but not to petroleum products.
-
Ethylene-propylene Rubber (EPR) (working temperature: -50 ~ 150℃) is applicable to water, oil-free air, dilute acid, and other chemicals, but not to petroleum products. It’s usually used for seals dealing with refrigerants.
-
Nitrile Butadiene Rubber (NBR) (working temperature: -40 ~ 120℃) is applicable to petroleum products, air, animal or vegetable oil, and mineral oils, but not to hot water or hot dry air of more than 60℃.
-
Fluorocarbon (FKM) Rubber or commonly known under the name of VITON (working temperature: -20 ~ 250℃) is applicable to a variety of strong acids, petroleum, halo-hydrocarbon, grease, hydraulic fluid, vegetable, animal, and mineral oil-based products also air containing hydrocarbons.
-
Teflon (working temperature: -55 ~ 260℃) is applicable to oils, water, and steam. In addition to that, it also has high mechanical strength and a very low friction coefficient -- which gives it a lubricating property. For this reason, Teflon is a suitable material for wear rings, guide rings, and check rings.
-
Nylon (working temperature: -40~120℃) is applicable to water, oil, and most chemicals. It also has a very low friction coefficient, enabling its usage without any additional lubricants. Similar to Teflon, Nylon is also used for guide rings, support rings, verge rings, and check rings.
Classification and Application of Different Rubbers for Sealing
Comparing the different materials shown in the list above, rubber is one of the most common sealing materials. Depending on the materials used, different types of seals can be utilized for different applications. One of the most common types of seals used is the O rings.
Rubber seals have been widely applied in many fields, such as in the chemical industry, military and defense industry, mining, transportation, petroleum, metallurgy and machinery manufacturing, and also other manufacturing industries. This being said, different types of rubbers should be present for different uses.
Common rubber compounds and mixtures for seals:
- Nitrile Butadiene Rubber (NBR) Seals: Applicable for usage in mediums such as petroleum hydraulic oils, glycol hydraulic oils, diester lubricating oils, gasoline, water, silicone grease, and silicone oils. It is one of the most widely applied rubber seals that have the lowest cost. It is not applicable to polar solvents, such as ketones, ozone, nitro hydrocarbons, MEK, and chloroform. Generally, its applicable temperature range is -40 ~ 120 ℃.
Photo by: Getty Images
- Hydrogenated Nitrile Butadiene Rubber (HNBR) Seals: It has excellent corrosion, tear, and compression deformation resistance. It can also withstand ozone, sunlight, and general weather conditions. It's better at withstanding abrasion and has a higher tolerance for heat when compared with common NBR materials. HNBR is commonly used for high-speed reciprocating and rotating seals of washing machines, automobile engine systems, and refrigeration systems with new environmental refrigerants with R134a applications. sing it in alcohols, esters, or aromatic solutions is highly not recommended. Generally, its applicable temperature range is -40 ~ 150 ℃.
-
Silicone Rubber Seals: Silicone rubber has fantastic resistance under ozone exposure and weathering conditions, with also the ability to maintain its unique flexibility under the working temperature of -55~250℃. It is suitable for manufacturing gaskets for thermal processes, also including seals for intense light sources and valve gaskets. A problem for its application lies in its tensile strength -- it’s not as good as general rubbers. Silicone rubber also has a poor capability of withstanding most concentrated solvents, oils, concentrated acids, and alkalis. Silicone seals are generally used in household appliances, such as electric water heaters, electric irons, and microwave ovens. The silicon rubber material itself can also be used for various products in contact with the human body as an insulation layer, such as kettles and water dispensers.
- FKM or VITON Seals: Along with its outstanding resistance to high temperatures (200~250℃), VITON also has excellent weather, ozone, and chemical resistance. Unlike silicone, it can withstand most oils and solvents, especially acids, aliphatic and aromatic hydrocarbons, also animal and vegetable oils. VITON satisfies the sealing needs of diesel engines, fuel systems, and chemical plants in the form of o-rings, cup seals, gaskets, and rotating lip seals, with higher service life or shelf life than common NBR seals. However, using it for ketones, esters with low molecular weight, and nitrate compounds is not recommended. Generally, its applicable temperature range is -20 ~ 250 ℃.
- Fluorinated Silicone Rubber (FLS) Seals: Offering similar functionality to VITON and silicone rubbers, FLS works excellently in resisting oils, solvents, fuel oils, in both high and low temperatures. It’s also a suitable material for handling oxide compounds, aromatic solvents, and chlorine solvents. It’s often used in aviation, spaceflight, and military applications. However, exposing them to ketones and brake fluids (i.e. glycols) is not recommended. Generally, its applicable temperature range is -50 ~ 200 ℃.
- EPDM Rubber Seals: The properties of the EPDM rubber lies in its chemical structure. Its main chain is a full straight-chain structure without double bonds, with a diene chain as its side chain to enable it to be sulfured. EPDM rubber has excellent ozone, weather, heat, and chemical resistance (i.e. alcohol, acid, strong alkali, and oxidants) -- except for aliphatic series and aromatic solvents. Thus, using it for kitchen utensils or having it exposed to mineral oils isn’t recommended. It is also resistant to steam, which makes it a good material for producing steam diaphragms, which allows operations under 120℃. Despite having a poor adhesion and viscosity, EPDM has been widely applied in bathroom equipment, car radiators, and automobile braking systems, and household applications, including the accessories of washing machines and TV sets, as well as sealing products of doors and windows, also adhesive tapes for the profile of many complexes. Generally, its applicable temperature range is -55 ~ 150 ℃.
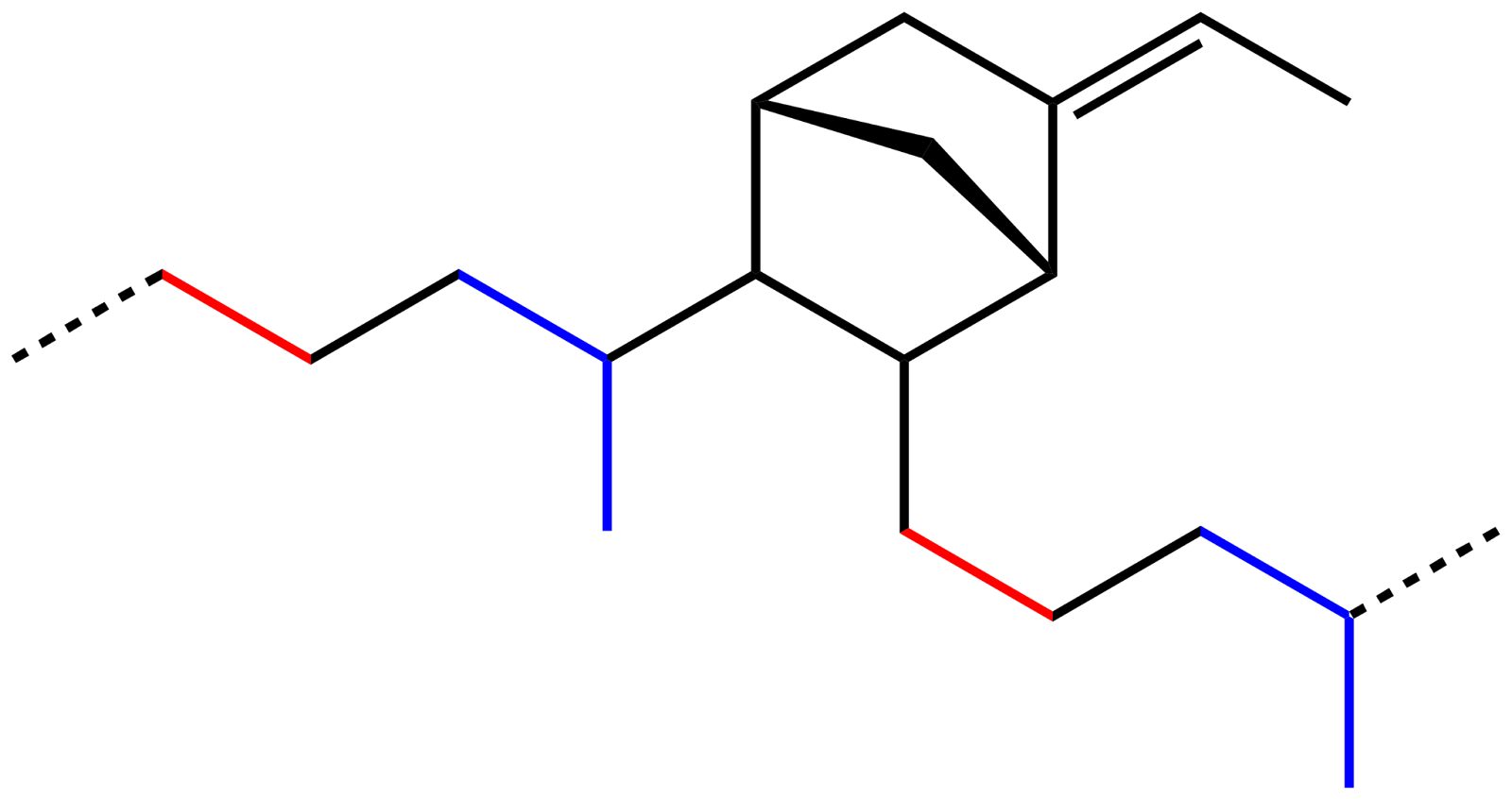
Chemical Structure of EPDM Rubber
Photo by: wikipedia.org
- Chloroprene Rubber (CR), or Neoprene Seals: Neoprene is commonly used to handle refrigerants like dichlorodifluoromethane and ammonia, as well as dilute acid and silicone grease, but it swells a lot in mineral oils with low aniline point. Neoprene crystallizes and hardens easily at low temperatures. It’s elastic with good air permeability and has fairly good resistance to air, sunlight, ozone, and direct flames - also handles chemicals well in sealed environments. Hence, Neoprene is usually used to manufacture diaphragms and vacuum sealing products. However, some chemicals, such as strong acids, aromatic hydrocarbons, nitro-hydrocarbons, esters, chloroform, and ketones, are not recommended for Neoprene applications. With a crosslinking and rupture temperature of above 200℃, Neoprene is usually used to manufacture sealing strips for doors and windows. Generally, its applicable temperature range is -55 ~ 120 ℃.
- IIR Butyl Seals: IIR Butyl seals are known for their great gas tightness and insulating properties. IIR Butyl rubbers are resistant to heat, sunlight, and ozone, and are generally used in contact with animal and vegetable oils, oxidizable substances, as well as polar solvents, such as alcohols and ketones. The seals are commonly used in chemical-resistant plants or vacuum equipment. However, butyl rubbers are not good materials for handling petroleum solvents, kerosene, or aromatic hydrocarbons. Generally, its applicable temperature range is -50 ~ 110 ℃.
- Polyacrylate Rubber (ACM) Seals: These offer excellent resistance to oils, high temperatures, and general weather conditions, but relatively poor mechanical strength, compressive deformation rate, and water resistance. ACM also corrodes with exposure to hot water, brake fluid (i.e. glycols), and phosphate ester. Hence it’s generally used in automobile transmission systems and power steering systems., working under high-temperature conditions, typically up to 175℃, and up to 200℃ for intermittent or short-term use. However, manufacturing these seals requires stretching and high compression stress techniques in really high temperatures, which is difficult to attain. Generally, its applicable temperature range is -25 ~ 170 ℃.
- Natural Rubber (NR) Seals: Natural rubber has better comprehensive mechanical properties when compared with synthetic rubbers: higher abrasive resistance, elasticity, and tensile strength. However, it oxidizes easily, becomes sticky when exposed to heat, swells, and dissolves in mineral oil or gasoline. NR materials have better resistance to alkali than to strong acid -- allowing it to be used in the liquids containing hydroxide ions, such as alcohols and automobile brake fluid (glycols and castor oil mixture) in the form of gaskets, cup seals, o-ring seals, or even sealants. Generally, its applicable temperature range is -20 ~ 100 ℃.
- Polyurethane (PU) Seals: PU rubber has better mechanical properties than other rubbers: it has a higher resistance to abrasion and is able to withstand higher pressure. In addition to that, it’s also very well resistant to oxidation and ozone, with an excellent capability to handle oils, though it is easy to hydrolyze at high temperatures, and damages with acid, alkali, water, steam, and ketones. It is usually used for systems running at high pressure and requires wear-resistant sealing, such as o-ring seals and diaphragm for hydraulic cylinders in for pneumatic systems. Generally, its applicable temperature range is -45 ~ 90 ℃.
Example of Seal Abrasion
- Epichlorohydrin Rubber Seals: Like NBR, Neoprene, and ACM, epichlorohydrin rubber performs well in oil, heat, ozone, alkali, water, and organic solvents conditions. However, it doesn’t perform well in lower temperatures. Epichlorohydrin rubber is commonly used for O-ring and various sealing rings, gaskets, diaphragms, and dust covers when their running temperature is not very low.

Valve Diaphragms
- Metal Rubber Seals: By its name, metal rubber seals are mostly made of stainless steel wire. Since it’s made from metals, it can be used in many environments, such as high vacuum, high and low temperature, strong radiation, and corrosive environments. Depending on their purposes and application pressure, the surface of the sealing rings could be made of different diameters and materials, such as stainless steel, copper, and Teflon. The ring usually has a coated metal rubber component, which is used as a liner, providing a high sealing strength and can enable continuous usage. Based on the type of metal combination used, its applicable temperature range is between -80 ~ 800 ℃. Although metal rubber sealing rings perform very well in an extensive application environment, their costs are relatively high in comparison with the regular rubber rings, hence are not as commonly used.