If you've been following us, you might have noticed that avoiding quality issues in your plastic molding production is a major topic that we discuss in this blog. Today we come back to you with three issues: black specs, ejector pin marks, and drag marks.
Black Specs
What are Black Specs?
On transparent plastic parts, white plastic parts, or light colored plastic parts, black specs often appear during the injection molding production. The black specs on the surface of plastic parts can affect the appearance quality of products, resulting in a high rejection rate, waste, and high cost in the production process.
Reasons and solutions
The problem of black specs is difficult to avoid in injection molding and needs to be controlled from the raw material, crushed material, ingredients, feeding, environment, and production processes to reduce the spec rate. The main reason for the black impurities to appear is that the foreign material within the plastic melt will degrade at high temperatures.
The specific reasons and improvement methods are shown in the following table:
Problem
|
Solution
|
The raw material is mixed with foreign matter or the drying bucket is not cleaned
|
1. Check the raw material for dark spots;
2. The drying bucket should be thoroughly cleaned
|
Color pigment diffusion is poor, resulting in condensation point
|
Add diffuser or change the quality of the toner
|
Impure or contaminated water outlet
|
Good control of water outlet (best use dust free workshop)
|
The raw material of the superheated melt attaches to the inner wall of the cylinder
|
1. Thoroughly shoot remaining melt; 2. Clean the molding cylinder thoroughly; 3. Lower melt temperature;
|
The mold gate is too small, injection speed is too fast
|
1. Increase gate size; 2. Make the injection speed lower;
|
Debris in the barrel causes the material superheated decomposition
|
Check the nozzle, ring and feed tube for wear/corrosion or replace the machine;
|
Dust falls into the air during mold opening
|
Adjust the wind and wind direction of the cooling fan (it is best to turn off the fan), cover the injection molding machine with film
|
The nozzle is blocked or the nozzle tip is too small
|
Remove residue material or enlarge the hole diameter
|
Crusher/mixer not cleaned up
|
Thoroughly clean up the crusher/mixer
|
Ejector Pin Marks
What are Ejector Pin Marks?
When the plastic part is ejected from the mold, the ejector pin will often leave deep or shallow traces on the plastic part. These traces can be shallow enough and away from the product face. In that case they can safely be ignored. But when these marks are causing non-uniform, deep, asymmetric marks on the part surface.
Examples of this issue are shown below:
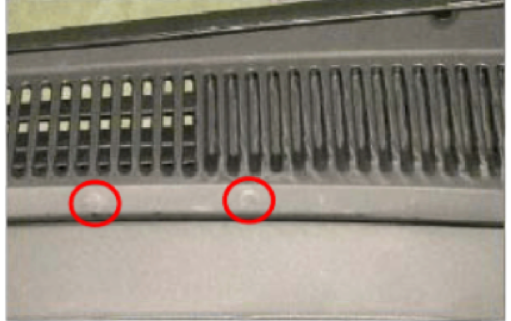
Reasons and Solutions
Problem
|
Solution
|
Ejection speed too fast
|
Make ejection speed lower
|
Excessive injection pressure or holding time
|
Reduce the pressure appropriately
|
Terminal injection speed too fast
|
Slow down injection speed towards the end.
|
The mold temperature is too low or too high
|
Adjust the mold temperature appropriately
|
Draft angle too small
|
At least 0.5 degrees draft on all vertical angles
|
Unbalanced runner system
|
Artificially or or naturally balance the mold.
|
The ejector pin is not in sufficient quantity or position
|
Increase ejector pin number or change ejector pin position
|
Air trapped in mold
|
Ensure venting is adequate
|
Thin walls where the ejector pin marks appear
|
Increase wall thickness where the marks appear.
|
The ejector pin size is too small or the ejection speed is too fast
|
Increase ejector pin size or slow down ejection speed
|
Drag Marks
What are drag marks?
When a part is being ejected from the mold, sometimes its surface can suffer from abrasion if the ejector system is not alligned or the draft angles are not sufficient enough to remove the part from the mold within allowed resistance.
This is shown in the following picture:
Reasons and Solutions
The main reason for drag marks to occur is a misaligned ejector system. In some cases the mold needs to have some tool work done on it and sometimes it needs to be changed completely with a better mold design.
The specific reasons and improvement methods are shown in the following table:
Problem
|
Solution
|
Flashing on the side of the mold cavity
|
polishing the surface of the mold cavity and removing flashes
|
Draft angle is not enough
|
Increase the draft Angle of the die cavity
|
The inner side of the cavity is too rough
|
Change rough grain to fine grain or smooth step structure
|
Excessive clamping force (mold cavity deformation)
|
Reduce clamping force and prevent cavity deformation
|
Front mold temperature is too high or cooling time is not enough
|
to Reduce cavity temperature or extend cooling time
|
The mold opens too quickly
|
Slow down the mold opening starting speed
|
Mold locking end too fast (mold cavity impact collapse)
|
Slow down the terminal locking speed to prevent the cavity from collapsing
|
Excessive injection pressure or hold-in duration
|
Reduce injection pressure or hold-in duration
|
Free Resource: 20 Most Common Problems in Your Plastics Manufacturing
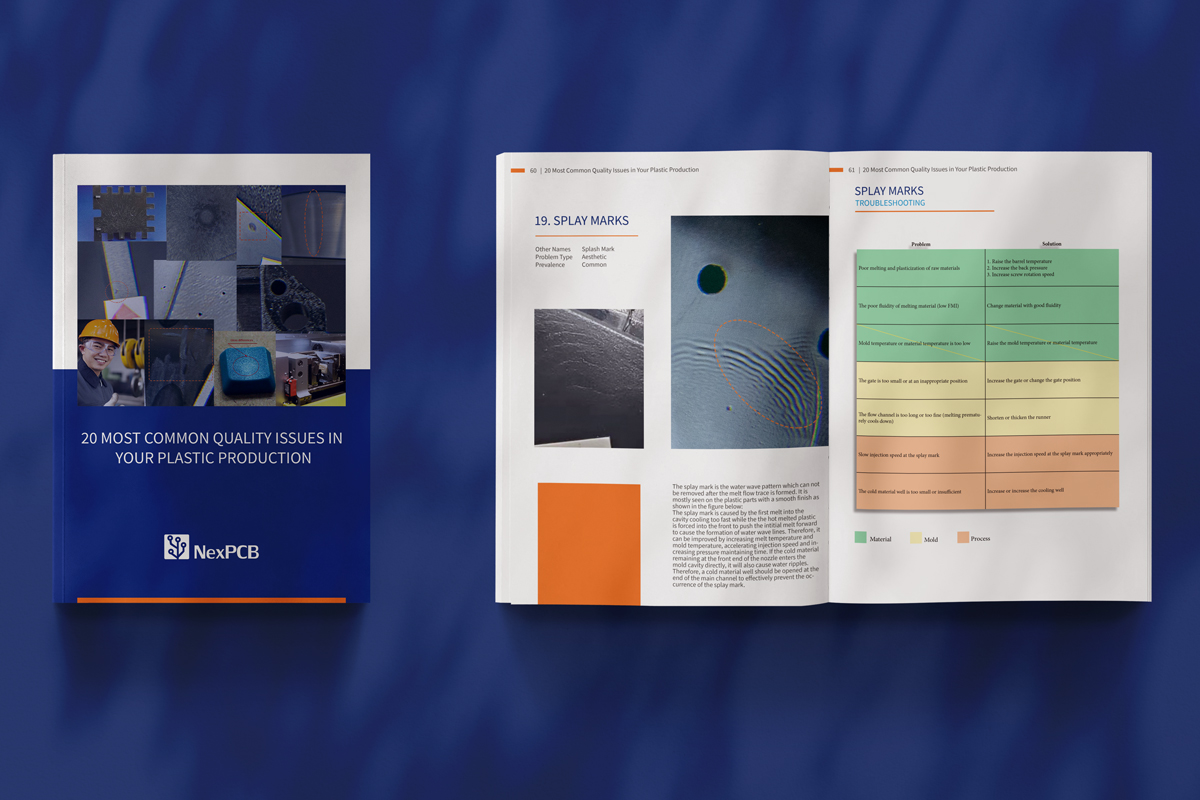

Have a project where you'd like professional help with your plastics? We're always happy to help! Press the LAUNCH button on top of this page and introduce us to what your manufacturing goals are. Alternatively, you can contact support if you need to shoot a question! If you have a specific project and can share the 2D/3D files with us, then you can submit a project request and our engineers can take a look and get you a quote!