Creating plastic casing using the injection molding process is more and more common during the development of a new product. However, a lot of quality issues might appear during the production process and might result in a loss of time and money. When dealing with plastic production, it's exceptionally important to understand what aspect of the production needs your attention and, most of all, how to deal with it. Today we will examine the short shot issues.
We call this phenomenon a „short shot” due the fact that it is caused by the molding shot falling short of filling the mold. In other words, the melted plastic can’t manage to occupy all the space designed by the mold and creates an unfinished and deficient product.
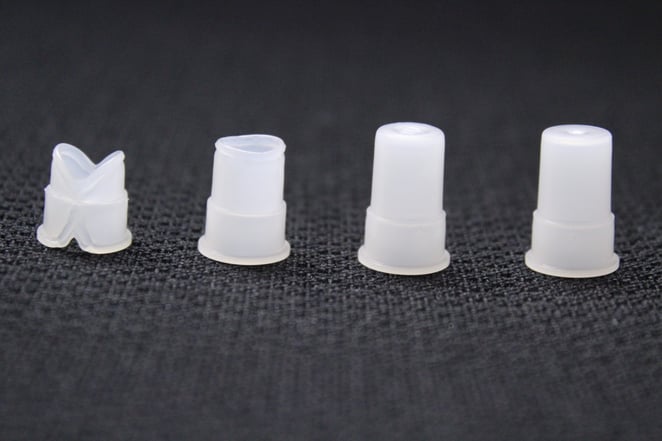
Maybe you have experienced this issue before and might be asking yourself : "Why are my parts giving up halfway?" or "How could I avoid it?" This can be due to several reasons that we will outline here.
Reason 1: the equipment is not suitable
Each plastic injection molding machine has its own injection rate. It might happen that your machine's injection rate is too low regarding the mass of plastic needed.
What can you do?
In this case, the only solution is to change the equipment. It is highly recommended to choose an injection equipment that, at least, proposes an injection rate 15% more than the injection volume needed (for both plastic and condensed material).
Reason 2: The Material Exhibits Bad "Flowability"
In injection molding, the flowability of the used material might impact the result and the quality of your product. More flowable your material is, easier it will be injected. If your material is not flowable enough, you might experience a Short Shot.
What can you do?
To solve this issue, you can either act on the material or on the injector. You can improve the placement of the runner, enlarge the gate or the size of the nozzles as a few examples. For the materials, you can also put some additional ingredients in the raw material to make its flowability better.
Reason 3: Excessive use of Lubricants
If lubricants are needed, an excess of it might make the changes of a short shot higher.
What can you do?
You can either reduce the amount of lubricant or make some adjustment spaces between the cylinder and the screw.
Reason 4: The Runner is Blocked by a Cold material
After some uses, some residual materials might obstruct the runner and contribute to bad circulation of the material (as shown on the picture below).
What can you do?
In order to resolve this issue, Disassemble the mold and injectors to clean the nozzles of any cold slug formations. A larger sized runner may also be needed
Reason 5: Bad Mould Venting
Another cause for a short shot is when there isn't enough space for the gases in the mould to escape quickly enough to prevent bubbles or other abnormalities in the moulded part.
What can you do?
Reposition the vent to a suitable place and potentially increase the size of vent (We prefer depth 0.02-0.04mm, width 5-10mm).
Reason 6: Melt Temperature is Too Low
If the melt's temperature is insufficient, the material will not be able to go through all the injection process and will definitely cause a Short Shot.
What can you do?
The temperature of the melt must be suitable and you can increase time of injection to improve this defect too. Make sure to consult the manufacturers datasheet on the minimum melt point of the plastic.
Reason 7: Mould Temperature is Too Low
More than the temperature of the material, you should also care about the mould temperature. That allows for better flowability of the material
What can you do?
You can preheat the mould to the temperature of process requirement before the injection machine starts; if the temperature of the mould can’t reach the target you should check in the cooling system.
Reason 8: The Injection Speed is Too Slow
The mold filling speed is related to injection speed, if the mold filling speed is too low the temperature of the melt is reduced so that the flowability is affected where the product will suffer from this effect.
What can you do?
You have to increase the injection speed appropriately
Reason 9: The Structure of the Plastic Part Design is not Manufacturable Enough
If the scale between width and thickness of the plastic is too large and the shape of plastic is complex, the flowability of melt will be suffocated at the thin wall of the part so the short shot might form as a result.
What can you do?
According to our experience, the best thickness of plastic is around 1-3mm and the large plastic parts is 3-6mm. The thickness of plastic becomes challenged if the thicknesses are more than 8mm or less than 0.5mm, so it's best to stay within these tolerances.
Free Resource: 20 Most Common Problems in Your Plastics Manufacturing
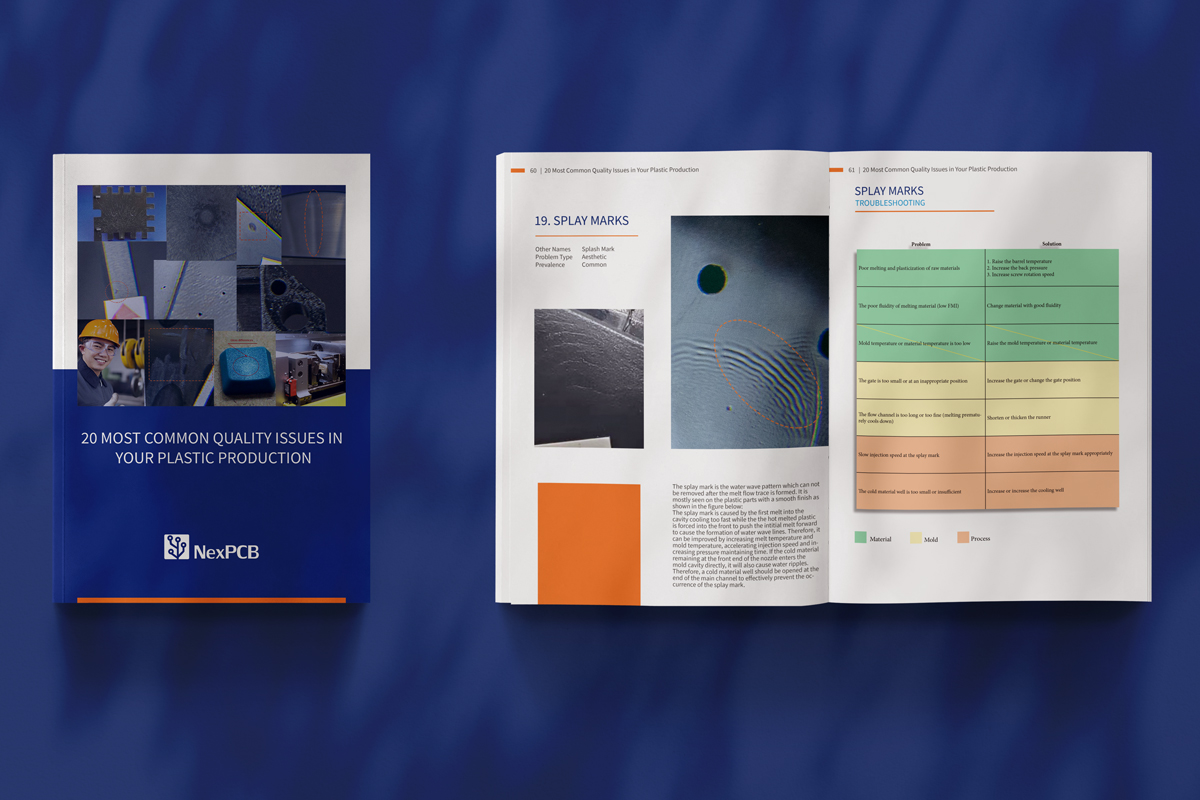

Have a project where you'd like professional help with your plastics? We're always happy to help! Press the LAUNCH button on top of this page and introduce us to what your manufacturing goals are. Alternatively, you can contact support if you need to shoot a question! If you have a specific project and can share the 2D/3D files with us, then you can submit a project request and our engineers can take a look and get you a quote!