There are a large number of variables that dictate good aesthetic and functional qualities to a product, and the optimal solution doesn't always lie in perfection in every way. It is about understanding your time-to-market requirements and acceptable quality thresholds that different aspects of your product can sustain. Today, we will discuss what aspect of production at what stage affects Product Quality.
Production Stages
Product Design
Like the importance of a solid foundation for an architectural structure, the effects of the decisions made in the product design stage will carry onto the later stages of product development. Not only design should be updated according to changing production methods at different production quantities, the gamble involving aesthetics, functionality, cost-economics and manufacturability should also be well played. Depending on the manufacturing method, what is suitable for one may be much lower yield in another. Therefore, we couldn’t stress the importance of continuously performing Design-for-Manufacturing in the early stages of development and every time something changes in your production method.
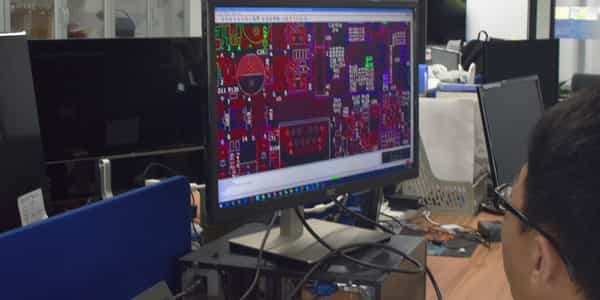
Incoming Materials
Any great design can be ruined due to a bad selection of materials. That’s why incoming materials are the single most important In a perfect world you would always be getting what you paid for, but in reality, some factories and material suppliers will try to get flexible with the selection of materials to lower their costs or use substitutes that they have in stock. Although this can indeed help reduce production costs and reduce delivery time, its effect on quality and final cost must be discussed with the customer in-depth.
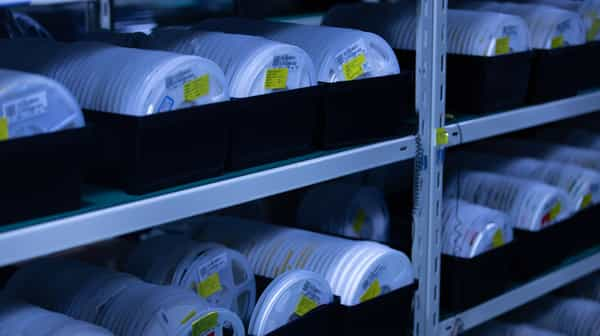
Manufacturing Processes
Manufacturing processes offer a large number of variables that can affect the product quality. The staff’s handling of tools and materials, the state and the quality of the machinery, the way manufacturing and assembly lines are configured… We even had experience with ambient temperature and humidity in different seasons affecting product quality in different ways!
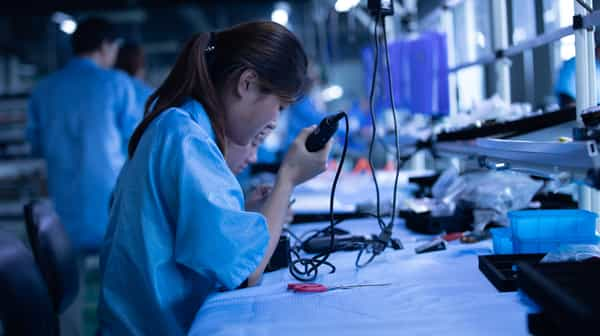
Storage & Transportation
Although packaging and shipping related errors don’t account for the most common of all quality issues, they tend to be the most costly and wasteful ones. With each additional step in production, the time and costs add up. So if your products were to be damaged during transit, there would most likely be no way to put a finger on them until you (or your end-customer) received them. You wouldn’t want to send defective products to your customers now, would you?
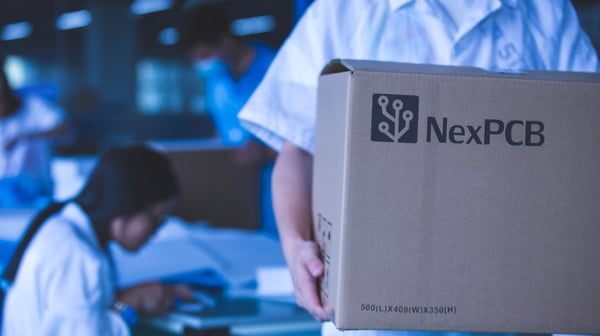
Now that you know the link between QC and major steps of manufacturing, you should be able to keep an eye on how your contract manufacturer is handling these processes. Although trust plays a pivotal role in working with manufacturing partners, transparent and timely sharing of QC-related information will make sure that expectations are well set and subsequently well met. If you're interested in how we handle QC objectives according to ISO-9001:2015 standards, visit the second chapter of our Quality Control blog series down below:
Step-by-Step Guide to Quality Control