Solder paste printing is a key part in the SMT (Surface Mount Technology) process. Since the solder paste is a mixture of powder and flux, it is fluid during the printing process. Viscosity is a major indicator of the form of solder paste fluids. If it has low viscosity, it flows easily for filling and collapses. If it has high viscosity, it is easy to roll, peel and form. The viscosity requirement is also different at different stages of solder paste printing. SMT has a flexible requirement of viscosity but fortunately viscosity itself is a variable that is easy to change. This requirement of varying viscosity places a higher dependence on the solder paste printing process and the printer's parameter settings.
In a solder paste printer, the printed solder paste is sometimes really thin, which results in damages to the product due to the small amount of solder paste after the furnace is completed. This is why it's very important.
1. The quality of steel plate
Stencil printing is contact printing, so the thickness of the stencil and the size of the opening determine the amount of solder paste needed to print. Too much solder paste will produce a short circuit, whereas too little solder paste will produce solder shortage at the solder joints,the template and shape of the opening and the smoothness of the opening which can also affect the quality of the release. Additionally, the template opening must have a bell-shaped mouth, otherwise the solder paste will be removed from the chamfering of the bell jar during demolding.
2. The printing process parameters
Solder paste is a thixotropic fluid. When the paste is viscous, the scraper will move forward at a certain speed and angle to push the solder paste into a roll in front of the scraper, resulting in the need to inject the solder paste into the pressure in the mesh or the leak hole. The viscous friction of the solder paste causes the solder paste to shear at the intersection of the squeegee and the stencil. The shearing force then reduces the viscosity of the solder paste thereby facilitating smooth injection of the solder paste into the mesh. There is a certain balance required between the speed, pressure and angle of the blade with the stencil and the viscosity of the solder paste. Therefore, the printing quality of the solder paste can only be assured by properly controlling these parameters.
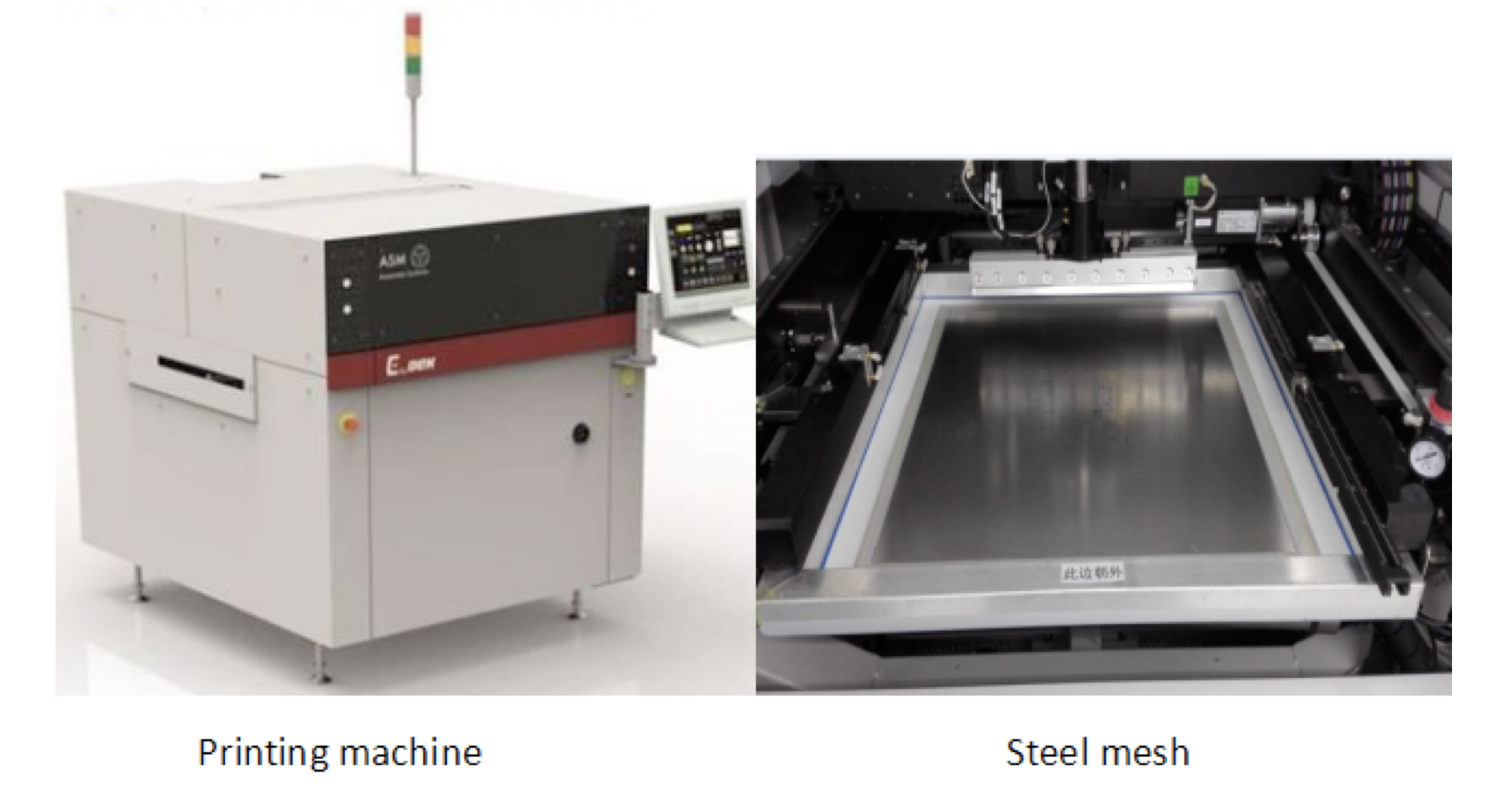
Different printing parameters can affect the volume of the solder paste. As the speed increases, the volume of the solder paste first increases and then decreases. As the pressure increases, the solder paste volume will increase and decrease quickly during the process. The faster the stripping, the larger the volume. The larger the gap, the larger the volume. The maximum value of the volume change of the solder paste is affected by many factors. The change caused by the speed and the grade are the largest variables. This is followed, in order of significance, by the printing gap, the peeling speed and the pressure as the least influential factor. For an SMT solder paste printing process it is important to keep in mind the effect each variable has. Proper engineering of these parameters can help produce appropriate stencils for your product, different tin thicknesses and more reliable quality.
Trying to manage your SMT production?
NexPCB might be able to help.
At NexPCB, we have the necessary SMT technologies for your PCB and PCBA production. We also offer other methods of PCB/PCBA such as THD (Thru-hole device) and THD and SMT mixed to suit your every need, from schematic to shipment done in 3.5 weeks. Learn more about our capabilities here.
In everything, we will make sure to produce the best quality product for you by full thorough inspection.
All the facilities are ISO9001 certified, with PCB assembly procedures to comply with lead-free and RoHS PCB assembly standards. Hence you can be assured of the quality of our work.
Just click the button below to tell us your project needs and our team would be glad to assist you!
