This post is the 8th article in our series about common issues that you can encounter during your plastic production. In this installment, we're talking about deformation (also called distortion). If you want to start from the beginning, you can check out our article on short shots.
What is deformation?
Deformation means that the shape of the injection parts is inconsistent with the requirements of the design drawings and shows some warping as in the pictures below:
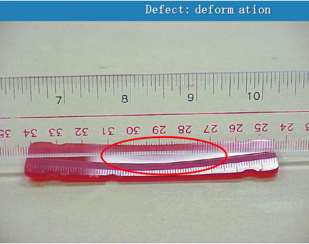
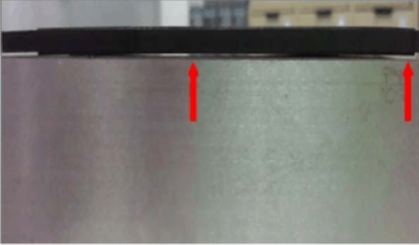
Deformation is usually caused by uneven shrinking of the plastic parts, exclusive of the deformation due to demold. The common deformation of plastic parts starts with the use of glass-reinforced plastic molding, large-area parts or very slender products. These have the highest likelihood of this problem forming.
Reasons and solutions
1. Improper cooling
Plastic parts are easily deformed due to improper cooling during the forming process. The structural design of plastic parts and the section thickness of all parts should be as consistent as possible. Enough cooling time must be maintained for the plastic parts in the mold. For the design of mold cooling system, attention should be paid to setting the cooling pipe at the place where the temperature rises and the heat is concentrated. For those parts that are difficult to cool, the cooling should be slowed down as much as possible so as to make the cooling of all of the plastic parts balanced.
2. Incorrectly designed mold pouring system
When determining the position of the gate, the melt should not directly impact the core and the force on both sides of the core should be as even as possible. For rectangular or flat plastic parts with large surface area, using molecular orientation, or plastic material that tends to shrink a lot, use of a film gate or multi-point gate should be adopted while side-gates should be avoided. For ring-shaped plastic parts, a disc gate or spokes gate should be used and side gate or spot-gate should be avoided. For shell parts, direct gate should be used instead of side gate.
3. Mold Release and Exhaust System Design
In terms of mold design, it is necessary to design the draft angle, position, and quantity of the ejection rod reasonably to improve the strength and positioning accuracy of the mold. For medium and small molds, the reverse deformation mold can be designed and manufactured according to the deformation rule. In mold operation, the ejection speed or ejection stroke should be slowed down appropriately.
4. Process setting is improper
The corresponding process parameters should be adjusted according to the specific situation.
As all solutions above, the causes of plastic deformation and improvement methods are shown in the following table:
Reasons |
Improvement method |
The finished product has not been cooled and set when it is pushed out |
1. decrease mold temperature
2. Extended cooling time
3. decrease material temperature
|
The shape and thickness of the finished product are asymmetric |
1. Use clamping device to fix after demolding
2. Change product design
|
The packing is overstuffed to form internal stress |
Reduce pressure and time |
Multiple gate feed is not equal |
The gate is improved so that the feed is balanced |
The ejection system is unbalanced |
Improve ejector system or change ejector mode |
The mold temperature is not even |
Improve the mold temperature so that the local temperature is suitable |
The plastic parts are sticky mold |
Repair molds and improve sticky mold |
The injection pressure or holding pressure is too high |
Reduce injection pressure or holding pressure |
Insufficient injection leads to shrinkage and deformation |
Increase the amount of glue shot, increase back pressure |
The front and back mold temperature is not comfortable, the temperature difference is large or unreasonable |
Adjust the temperature difference between the front and back dies |
Plastic shrinkage anisotropy is greater |
Use plastic with a low shrinkage anisotropy |
Improper delivery or packing |
Improve packaging and enhance protection |
Is quality something you care about in your production?
NexPCB cares about this too.
NexPCB places high importance on quality assurance and standards. We offer full inspection before shipping which includes structural reliability and performance testing. All of our facilities are ISO9001 certified. Learn more about our quality assurance technologies here.
You can be assured of the quality of your PCB/PCBA and SMT production.
Feel free to tell us your project needs and our team of experienced engineers would be glad to support you!

Come grab your free E book on Plastic Production issues and how to avoid them
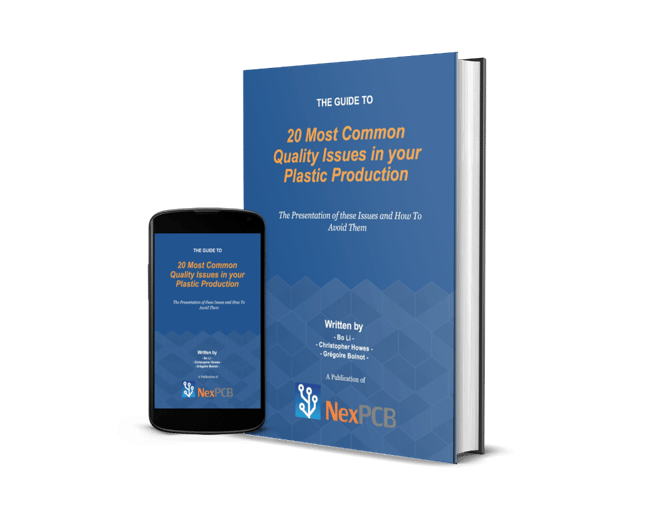