Today marks the last of our posts about common issues in your plastic production. This post belongs to a series aiming to describe the 20 most common issues you might encounter in your plastic production. If you want to start from the beginning, you can start here with our first post about short shot.
Color Streaks
What is color streaks?
The surface of the plastic part or the part where the flow direction changes will produce a local color deviation phenomenon, called color streaks (pictured below) :
There are many reasons for color streaks including uneven pigment diffusion during the injection molding process, incomplete cleaning of the barrel, mixture with other colors in the raw materials, the unstable proportion of recycled material, and poor melt plasticization.
Some ways to improve this defect are listed below:
Problem
|
Solution
|
Improper melt plasticization
|
Improve plasticity with additives or plastic quality
|
Pigment clumps or poor diffusion
|
Grind or replace the pigment
|
Too little dispersion aid
|
Properly increase the dosage of the dispersant or replace it
|
The compatibility of plastics and pigment is poor
|
Replace the plastic or pigment in masterbatch
|
Low material temperature or low back pressure
|
Increase material temperature, back pressure, and screw rotation speed
|
Unclean cylinder (containing other residues)
|
Thoroughly clean the cylinder
|
The inner wall of screw rod and feed tube of injection was damaged
|
Repair or replace damaged screw/barrel or machine
|
Residual melt is stuck on the head of the nozzle
|
Clean the residual melt on the outside of the nozzle
|
Gloss Differences
What are gloss differences ?
When the plastic part is formed, the finished surface can lose its original luster and form an opalescent film, or is in a fuzzy state. This is defined as having gloss differences.
An example of such error is shown below:
The surface gloss differences between plastic parts is mostly due to the surface state of the mold. If the surface of the mold is not polished well or has mold scale, the surface of the finished product will not get a good gloss. Excessive use of release agents or oil release agents is also a cause of poor surface gloss. If the material is hygroscopic or contains volatile or foreign matter mixed in (pollution), this can also cause gloss differences.
Specific analysis and improvement methods are as follows:
Reason analysis |
Improving methods |
Mold temperature is too low or material temperature is too low
|
Raise mold temperature or material temperature
|
The density of the melt is not enough or low back pressure
|
Increase pressure keeping pressure/time or increase back pressure appropriately
|
Excessive mold release agent in the mold
|
Control the amount of mold release agent and wipe it clean
|
The surface of the mold is permeated with water or oil
|
Wipe clean water or oil and check for leakage or oil
|
The inner surface of the die is not smooth
|
Mold polishing or removing glue stains
|
The raw material is not sufficiently dry
|
Fully dry ingredients
|
Mold cavity with mold scale/glue stain
|
Remove mold scale/glue stain from the mold cavity
|
The molten material decomposes overheat or stays in the cylinder for too long
|
Reduce melt temperature or residue
|
Too small runner and gate (cold material)
|
Increase the size of runner and gate
|
Injection speed is too slow or the mold temperature is uneven
|
Improve injection speed or cooling system
|
The cylinder is not cleaned
|
Clean the cylinder thoroughly
|
The cylinder is not cleaned
|
Clean the cylinder thoroughly
|
Excessive mold release agent in the mold
|
Control the amount of mold release agent and wipe it clean
|
The raw material isn’t dry enough
|
Fully dry ingredients
|
Mold temperature or material temperature is too low
|
Raise mold temperature or material temperature
|
Free Resource: 20 Most Common Problems in Your Plastics Manufacturing
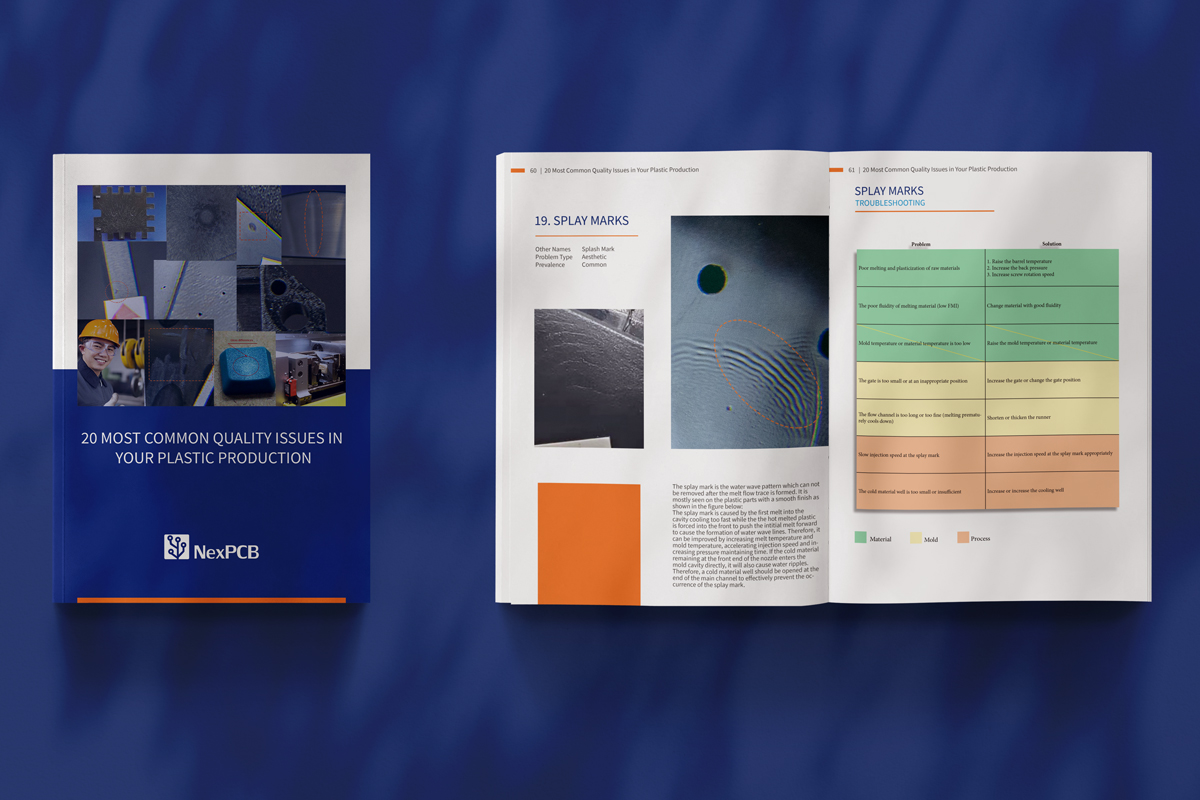

Have a project where you'd like professional help with your plastics? We're always happy to help! Press the LAUNCH button on top of this page and introduce us to what your manufacturing goals are. Alternatively, you can contact support if you need to shoot a question! If you have a specific project and can share the 2D/3D files with us, then you can submit a project request and our engineers can take a look and get you a quote!