After you’re done brainstorming your ideas, then designing, simulating, and finally, creating prototypes for your hardware project, you’ll need to conduct validation tests on your product.
The validation tests are done in distinct 3 stages:
- EVT (Engineering Validation Test)
- DVT (Design Validation Test)
- PVT (Production Validation Testing)
The journey to launching a product always involves risk. Like going from just doing a simple brainstorming process to creating a solid multi-part prototype, you’ll be taking on more risk as you go further into the journey. This also occurs in the validation testing phase. As you go from EVT to DVT and to PVT, you’ll be producing a larger batch of products, exposing you to more risk. Hence, thorough inspections must be done in every step to ensure that the risk will be minimized at the deeper levels.
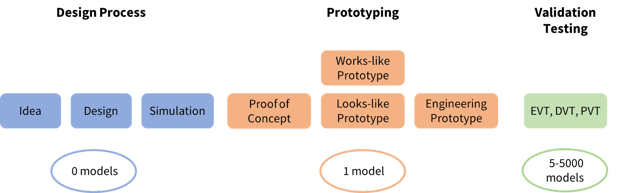
During these validation testing processes, personnel from different departments of the team should all be involved. The issues faced in these processes should be viewed from different backgrounds.
For example, the production of a part of the product takes too much time. Here, engineers should find the source of the problem and propose a solution. The finance department will weigh down the cost of production: budget and time-wise. The supply chain will find any alternative for materials or off-the-shelf parts. The management will ensure that this runs efficiently in a timely manner, protecting the team structure and making sure that the goal and vision of the product are kept.
EVT (Engineering Validation Test)
During the Engineering Validation Test (EVT) process, you’ll be faced with various issues regarding the product's operations and functions that need to be solved. Hence, before EVT, you’ll be expected to present an engineering prototype, which is a combined looks-like and works-like prototype. This engineering prototype should already have each of its individual features independently studied. Here say, the task of the EVT is to ensure the features all work in the said model.
EVT is carried out to qualify if the engineering prototypes have met the customer’s initial requirements and get rid of potential hardware failures. Unlike engineering prototypes, prototype parts undergoing EVT should be made with the intended materials and through the planned manufacturing processes.
Throughout the process of EVT, each of the product’s parts will be manufactured as was planned for the final product. These parts, along with the other off-the-shelf parts, will be assembled together, before being tested. The product then will be tested as a whole for its functionality, i.e., mechanical movement, power consumption, data transmission processes, and other mechanisms or workflows.
DVT (Design Validation Test)
After you’re done with EVT, you can move forward to carry out DVT (Design Validation Test). During DVT, more prototypes will be produced than what was produced during the EVT process. DVT assures that the products being manufactured are done with the required quality. The consistency in tooling and manufacturing techniques is keenly monitored here.
Basic production checks, such as the tooling processes and manufacturing techniques are inspected to ensure that the production meets the environmental and legal regulations. Certification processes and further testing (such as aging, thermal, chemical resistance, etc.) are performed with DVT models.
The process of conducting DVT is compulsory not only to comply with the regulatory requirements but also to realize the product. Finding a balance between the product’s quality, functionality, cost, and pricing should be weighed here. Make sure your product is both feasible to manufacture and able to compete in the market.
During the process of DVT, around 30 to 100 pcs of products can be made, but the value ranges based on the complexity and the cost of the product (manufacturing and tooling process, materials, other parts, etc.). The batch produced for DVT should be large enough to observe the potential problems, but not too big that it’ll cost a large part of the product’s development budget.
PVT (Production Validation Testing)
PVT (Production Validation Testing) is the last process before the pilot run. This means the products will be produced with the final selection of machinery, through the fixed process procedures, with the set tooling and materials.
Since PVT is the final testing operation before the production, all aspects of the manufacturing process must be finalized. you should have developed both your quality assurance (QA) and quality control (QC) procedures. This will be essential for your future production when you’re working with a contract manufacturer. Your quality control process will highly rely on your DFX (Design for Excellence) strategy. A completed DFX strategy will be expected to have an efficient DFM (Design for Manufacturing) and DFA (Design for Assembly), to minimize the output error rate. The faulty rate of products produced at this large batch realistically can’t be 0 like what was done in the prototyping processes, EVT, or even DVT. Pushing the management of non-conforming products and materials to be set as one of the priorities in PVT.
At the PVT stage, companies generally produce around 5-10% of their planned first official run output. At this phase, testing is carried out to ensure that your product can be processed at the said volume for the target time while retaining its quality level and costs. Planning for mass production deployment should also be thoroughly planned, from manufacturing processes to packaging design up until the shipment processes.
The validated output of this PVT process will be considered fit for selling. The products at the end are qualified to be published for potential investors to learn more about your product and thus give you the opportunity to get funding for your project.
Now that you've learned about the various validation and testing processes, what's left is just to launch your product. We're here to assist you to design, manufacture, and assist you with the problems you face along the processes, from design, to prototyping, to your launch. Feel free to contact us, we'll be more than glad to help!