Today, we continue our journey of exploration into the common issues that happen in plastic production. This time we will take some time to get how to avoid jetting and air lines! Want to know more about other common issues? Check out our blog post about you are seeing weld lines in your parts.
What is Jetting?
The Reason:
If the melt is injected too fast at the gate, the surface of the parts (in front of the edge gate) will produce a serpent-shaped line. This is commonly called jetting.
Jetting mostly occurs with edge gates. When the plastic melt flows through the nozzle, runner, gate, and other narrow areas at high speed, it suddenly enters the open and relatively wide areas of the mold where the melt material will bend forward along the flow direction like a snake. The molten plastic will then cool down quickly after contact with the mold surface. Because this first-to-enter part of the material can’t have good fusion with the rest of the resin subsequently entering into the cavity, this phenomenon results with a visual defect.
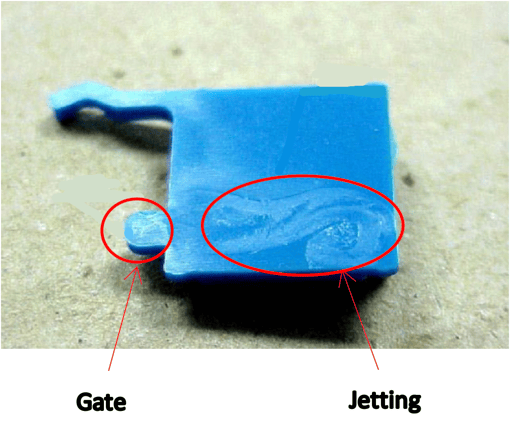
The Solution:
Most of the jetting is found when the gate type of the mould is side gate. When the plastic melt flows through the nozzle, runner, gate, and other narrow areas at high speed, it suddenly enters the open and relatively wide area of the mold where the melt material will bend forward along the flow direction like a snake. The molten plastic will then cool down quickly after contact with the mold surface. Because this part of the material cannot have a good fusion with the subsequent resin into the cavity, the result is a clear spray on the product. Under certain conditions, the melt in the early stages come in at a relatively low temperature when expelled from the nozzle so, before the contact surface of the cavity, the melt viscosity is very high. As the lower temperature resin flows in like a snake, the as the higher temperature of subsequent melt comes into the cavity unceasingly, it causes the initial melt extrusion to be deeper in the mold leaving a jetting form.
The reason and improvement method of injection pattern are shown in the table:
Reasons
|
Solutions
|
1. Improper placement of gate (Direct injection into the cavity)
|
Change gate position (Move to the corner)
|
2. The material temperature or mold temperature is too high
|
Reduce the material temperature and/or mold temperature
|
3. Injection speed is too fast (in-gate)
|
Reduce the injection speed
|
4. The gate is too small or unfit for application (side-gate)
|
Employ a wider gate
|
5. Plastic is has very high viscosity
|
Change the plastic raw material with a lower viscosity one. (Higher the viscosity, more the jetting)
|
What is Gate Blush?
If the gate is too small and the injection speed is too fast, the melt flows violently and pulls air into the melt. This will leave cloudy marks in the gate location, turning points, and step positions of the plastic parts. It’s easiest to see gate blush at the gate with materials like ABS, PC, and PPO.
The picture of a red plastic part here shows this condition:
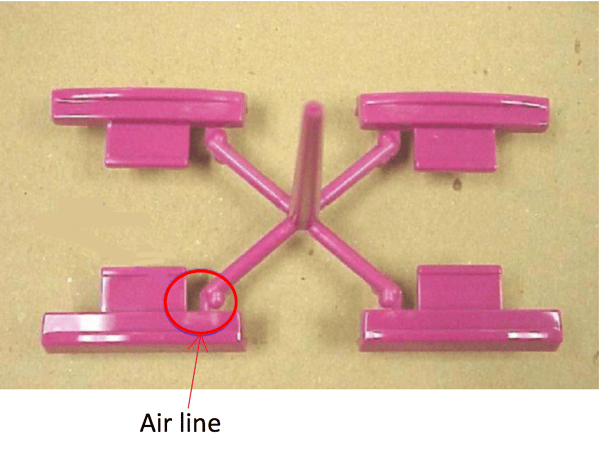
The reasons and ways to improve gate blush are as follows:
Problem
|
Solution
|
The gate is too small or improperly positioned
|
Increase gate size or change gate position
|
Excessively long or thin runners (melt is easy to cool)
|
Shorten or widen runners
|
Air trapped within mold due to bad vent
|
Adjust the mold vent
|
The cooling channel is too small or insufficient.
|
Increase cooling fluid or enlarge the cooling channel, or place channel near the largest part of the mold
|
Can’t figure out maximum injection temperature required with the current mold setup
|
Moldflow simulation can help target the right gate size and wall thickness at the inlet
|
The injection speed is too fast
|
Multistage injection of material to slow down the injection speed of corresponding parts
|
Raw materials are not fully dried or are decomposed by overheating
|
Fully dry the raw materials and don’t use thermoset materials
|
Free Resource: 20 Most Common Problems in Your Plastics Manufacturing
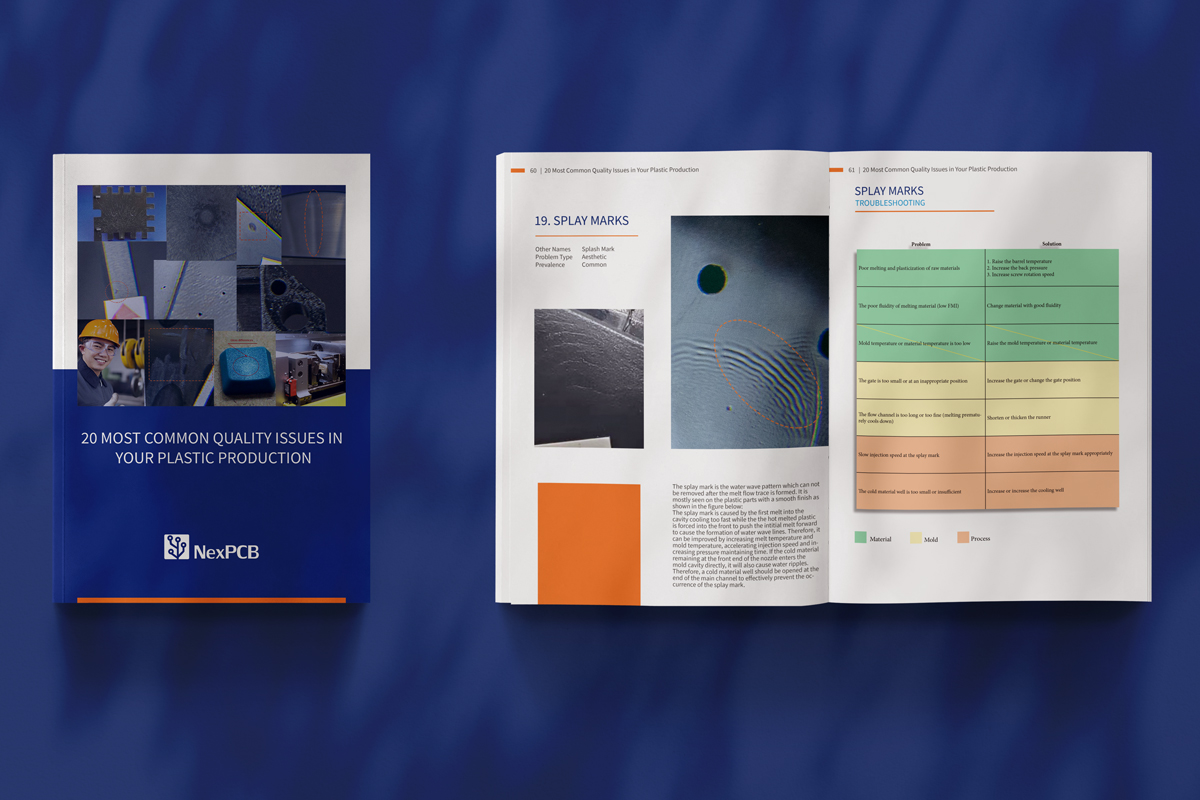

Have a project where you'd like professional help with your plastics? We're always happy to help! Press the LAUNCH button on top of this page and introduce us to what your manufacturing goals are. Alternatively, you can contact support if you need to shoot a question! If you have a specific project and can share the 2D/3D files with us, then you can submit a project request and our engineers can take a look and get you a quote!