After analyzing the short shot issue, We decided to come back to another problem you can encounter during your injection molding plastic production: Sink Marks.
What is a Sink Mark?
During the injection process, there are times when parts of the mold don’t get enough pressure to set the plastic. When this happens, it can cause additional stress on that area where the rate at which the plastic shrinks is slower than other areas. The sink marks appear when the surface of the plastic is pulled in by this stress because the surface isn’t solid and the melt isn’t complete.
What is the reason ?
As you can tell, the sink marks will not only make the appearance bad but also the strength low on the surface. The sink mark has close relationship with the material of plastic product, injecting manufacturability, and the structure of plastic product or mould.
1. The Material of the Plastic Product
Different materials have different shrinkage rate. The materials that are most likely to have sink mark mostly belong to crystalline plastic products, such as polyamide (PA) and polypropylene (PP). When the crystalline plastic is heated to be in a fluid state during injection, the volume shrinkage of the product can be higher than expected. This can cause the size to be irregular and cause sink marks.
2. Injection Molding Manufacturability
There are many reasons that can lead to a sink mark with respect to injection molding manufacturability. Issues such as insufficient holding pressure, insufficient injection speed, low temperature of the mold or material, and insufficient clamping pressure or duration are all elements that can contribute to occurrence of sink marks. The structure of the plastic product or the mold can have an impact as well.
Non-uniformity of the plastic parts’ wall thickness is the primary cause of a sink mark. One typical example is found on plastic surfaces with a rib or a brace.
How to solve it?
According to the above analysis, you can see the how making the improvements below can solve problems with uneven shrinkage:
Reasons
|
Solutions
|
1. Insufficient amount of resin injected into the mold
|
Increase the charge of resin into the mold
|
2. Improper material temperature (too high or too low)
|
Adjust material temperature (see material data sheets)
|
3. Improper mold temperature
(too high or too low)
|
Adjust mold temperature (correction)
|
4. Insufficient cooling time
|
extend cooling time before ejecting from the mold
|
5. Bad mold exhaust at sink mark
|
Modify the exhaust vent design
|
6. Wall thickness is too thick at rib or brace
|
Adjust the mold to make the wall thickness as uniform as possible within the design
|
7. Improper gate placement or the slow injection process
|
Increase gate number or place gate at a location where the wall is thicker
|
8. The nozzle is too narrow or too wide
|
Adjust nozzle width according to the design of the mold and the kind of material used.
|
Because the shrinkage rate changes according to different plastics, pay attention to the shrinkage rates of your chosen materials:
Material |
Shrinkage rate/% |
Material |
Shrinkage rate/% |
Material |
Shrinkage rate/% |
GPPS |
0.5 |
PA66 |
0.8~1.5 |
PC |
0.5~0.7 |
HIPS |
0.5 |
PA6 |
1.0 |
PMMA |
0.5~0.8 |
SAN |
0.4 |
PPO |
0.6~0.8 |
PVC(hard) |
0.1~0.5 |
ABS |
0.6 |
POM |
1.5~2.0 |
PVC(soft) |
1~5 |
LDPE |
1.5~4.5 |
CAB |
0.5~0.7 |
PU |
0.1~3.0 |
HDPE |
2~5 |
PET |
2~2.5 |
EVA |
1.0 |
PP |
1~4.7 |
PBT |
1.5~2.0 |
PSF |
0.6~0.8 |
Free Resource: 20 Most Common Problems in Your Plastics Manufacturing
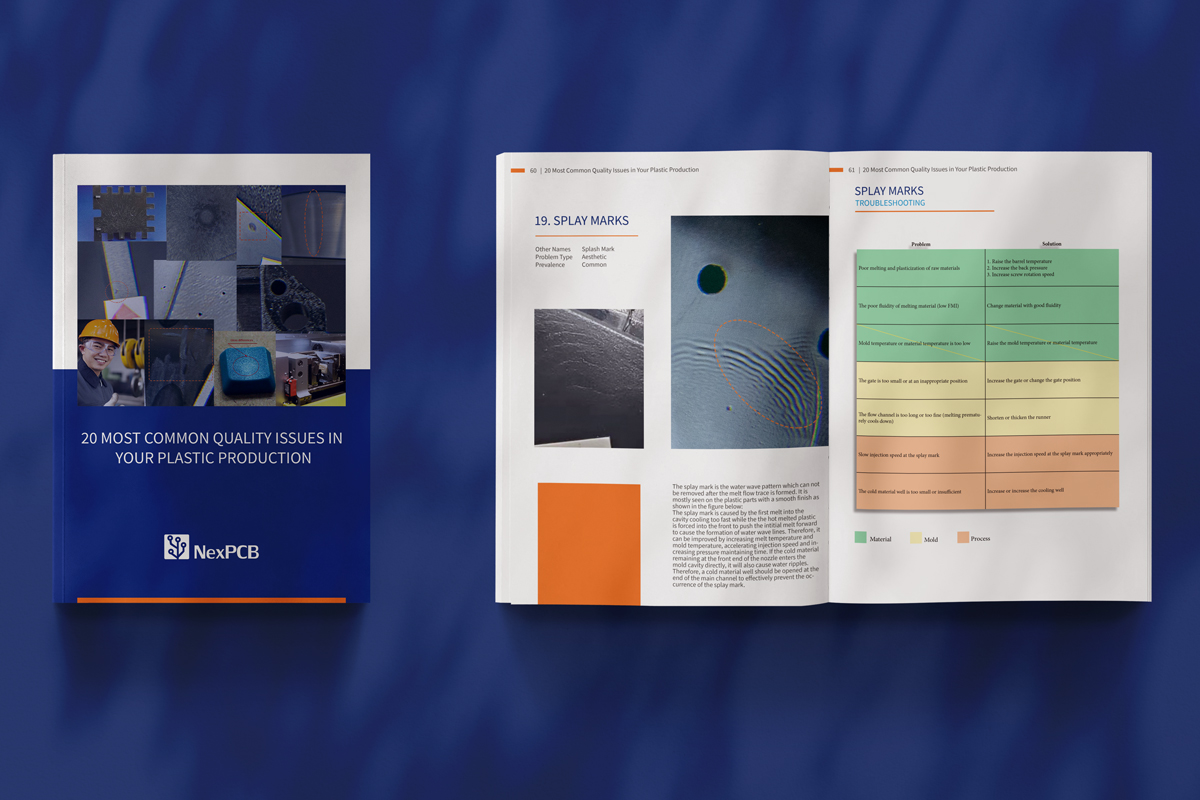

Have a project where you'd like professional help with your plastics? We're always happy to help! Press the LAUNCH button on top of this page and introduce us to what your manufacturing goals are. Alternatively, you can contact support if you need to shoot a question! If you have a specific project and can share the 2D/3D files with us, then you can submit a project request and our engineers can take a look and get you a quote!