After analyzing Short Shots, Sink Marks, Flashing and Bubbles issues, we decided to come back to some other problems you may encounter during your injection molding plastic production. This time, we'll talk about bulges and vacuum vesicles.
Blisters
What exactly are blisters?
There are times that, when a part has been manufactured and released from the mold, the surface has an area where the volume has expanded more than its surrounding area. This phenomenon is called blistering. Blisters elevate the surface of the product with a thin, film-like layer.
What causes blisters on plastic parts?
While the main culprit behind blisters is excessively high injection speeds, it is in essence caused by the air within the mold being unable to vent out. Before redesigning your vents, check whether slowing down injection fixes your issue.
This causes the "blister" look that characterizes this issue. You know, like the blister you get on your finger after touching the tip of a soldering iron by mistake. You can mitigate the formation of blisters on your plastic manufacturing by:
1. Ensuring effective cooling by making the temperature of the mold cooler, increasing the mold hold-in time, and/or decreasing the plastic injection temperature.
2. Make the mold injection speed slower, reduce molding cycle and/or reduce the flow resistance (through more fluid plastics, larger gates and nozzles).
3. Increase the pressure maintaining pressure and time.
4. Optimize the structure of plastic and avoid having areas where the plastic part is too thick or too thin.
Effectively balancing these variables can help in avoiding blisters in plastic.
Vacuum Voids
What is a vacuum void?
Shrinkage in the interior of a plastic part is often called a vacuum void. It is generally found in an area where the plastic is very thick or where multiple channels come together to form a rib or a wall. These areas are especially susceptible to uneven cooling or shrinking, which is the underlying cause of voids.
Below is a cross-sectional picture of what this looks like at an area where a plastic outer section has a small support ridge and a vacuum void has formed inside :
What causes the vacuum vesicle?
When the part is cooling down after the injection is completed, areas of thicker plastic will tend to dry at a different rate than thin ones. If the hardness of the plastic isn’t high enough or there isn’t enough fiber mixed into the raw material, voids can form within the plastic as it shrinks unevenly.
This particular problem can affect the strength and the mechanical properties of the plastic. If the plastic is transparent, it can also affect the appearance of the part as you'll be able to see the voids inside. The key point in remediation is the control the mold temperature and design. Some specific issues that can cause this problem and some ways to improve are below :
|
|
The mold temperature is too low
|
Increase the mold temperature
|
The wall thickness is too large (like the boundary of the rib or the brace to the wall)
|
Optimize the product structure design, try to keep the wall as thin as possible
|
The gate is too small or the location of gate is improper.
|
Make the gate larger or change the gate location
|
The runner is too long or too thin.
|
Shorten and/or enlarge the runner
|
Injection pressure is too low or injection speed is too slow
|
Increase the injection pressure or speed
|
Pressure protection or the time isn’t enough
|
Increase the pressure and cooling time
|
The melt temperature is too low or short shot
|
Increase the temperature or increase amount of material to melt
|
Cooling time in mold is too long
|
Decrease the cooling time in mold or use hot bath cooling
|
Back pressure is too low |
Increase overall back pressure on the mould |
Bubbles vs Vacuum Voids
What separates bubbles from vacuum voids is the lack of air. A simple heating test can reveal the exact issue. A vacuum void will create a debris while a bubble would burst outwards.
Free Resource: 20 Most Common Problems in Your Plastics Manufacturing
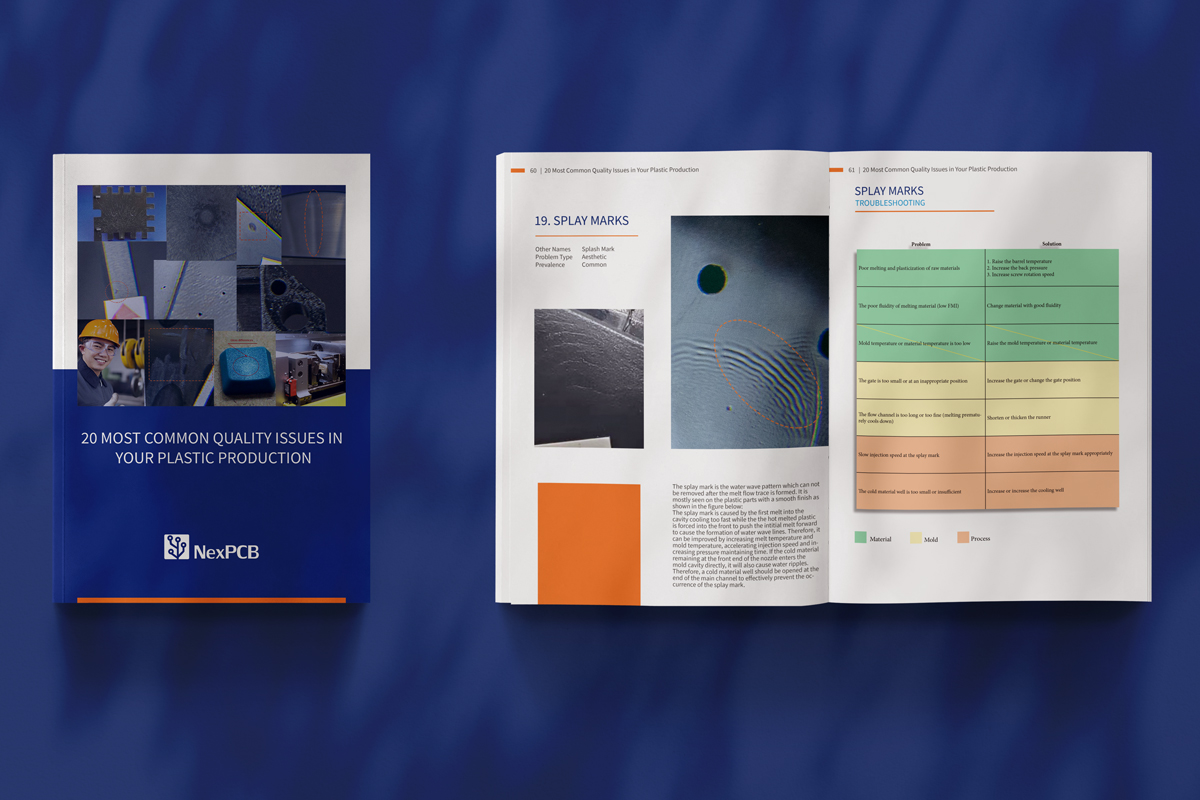

Have a project where you'd like professional help with your plastics? We're always happy to help! Press the LAUNCH button on top of this page and introduce us to what your manufacturing goals are. Alternatively, you can contact support if you need to shoot a question! If you have a specific project and can share the 2D/3D files with us, then you can submit a project request and our engineers can take a look and get you a quote!